Un IRM pèse en moyenne 6,4 tonnes, dont 2,7 de fer et 1,8 de matériaux non ferreux, essentiellement du cuivre. Globalement, 98 % de ces composants ont une haute recyclabilité.
« Plus de la moitié de la population mondiale n’a pas accès à un IRM, souligne Katharina Hessels, qui dirige l’Unité développement de la base installée chez Siemens Healthineers. Et le secteur de la santé équivaut au 5e pays émetteur de CO2 dans le monde. » Il y a donc un double intérêt, économique et écologique, à augmenter le cycle de vie des machines et de leurs composants.
Plusieurs mesures sont mises en place en ce sens. L’écoconception vise à faciliter le recyclage et l’évolution des machines, via le choix des matériaux et leur modularité. L’utilisation du mode EcoPower réduit la consommation électrique aux heures où l’appareil n’est pas en fonction. Mais c’est surtout sur le réemploi des IRM que le potentiel écologique est important. Chez Siemens Healthineers, leader du marché, quatre types d’approches sont proposées :
- L’upgrade léger : l’établissement conserve sa machine, mais une mise à jour est effectuée pour en faire évoluer les performances, par exemple sur le logiciel avec ajout de l’intelligence artificielle, ou pour l’adapter à un nouvel usage spécifique.
- L’upgrade lourd : l’aimant, composant principal, reste sur place, mais le reste de l’équipement est démonté et de nombreux composants sont changés : électriques, radiofréquence, ajout de nouvelles technologies, etc. L’appareil ainsi recomposé dispose d’un marquage CE propre, avec un nouveau nom et numéro de série. Dans la plupart des cas, il est considéré comme neuf par les autorités.
- La revente d’occasion, sur le marché secondaire, après contrôle de la machine par le constructeur, principalement vers des pays tiers en ce qui concerne la France, ou vers le marché vétérinaire et parfois la recherche.
- Le reconditionnement à neuf : seules les machines dûment entretenues et désinstallées par les experts du constructeur peuvent entrer dans ce circuit. Les machines, qui comportent 3 000 pièces, reviennent à Erlangen, y sont entièrement démontées sur une chaîne de production dédiée et les pièces sont testées sur place, et remplacées le cas échéant. L’aimant, qui est produit à Oxford, y est renvoyé dans son unité d’origine. Puis des machines dites Ecoline, sont recomposées « tout comme neuves », avec un nouveau marquage CE.
Aujourd’hui, la France est l’un des plus importants fournisseurs de cette filière de reconditionnement, du fait de la qualité de ses contrats de maintenance.
Ces différentes modalités dépendent des règlements mis en place dans chaque pays — certains interdisant l’import de matériel d’occasion — ainsi que du modèle économique des hôpitaux et cliniques (leasing, forfait technique, etc.).
En France, pour des raisons réglementaires, le reconditionnement reste anecdotique. « Le rôle du forfait technique est de compenser les charges liées à l’acquisition et à l’utilisation d’un équipement neuf. Cette nomenclature, qui diminue au bout de sept ans, contribue à maintenir un parc de machines performantes pour les patients français, car elle favorise l’installation d’équipements modernes. De fait, si notre parc en France peut pêcher en termes de volume (densité d’IRM par million d’habitants au regard des autres pays), il se situe parmi les meilleurs en Europe en termes de performances techniques », explique Veronica Luneau, responsable développement de la base installée en France chez Siemens Healthineers.
« Depuis peu, le comportement des acheteurs change, en grande partie du fait des directives de durabilité, et de la situation économique globale », souligne-t-elle, en reconnaissant toutefois que les clients français, que ce soit dans le public ou le privé, restent très friands de nouvelles technologies. « C’est un moyen de garantir des soins d’excellence, une bonne expérience patient et de profiter d’une bonne attractivité pour le personnel médical et paramédical, secteur en pénurie. »
Le choix des modalités d’évolution des machines peut aussi dépendre de contraintes plus techniques : dans les bâtiments historiques, quand l’établissement s’est construit autour de l’IRM, qu’un axe routier important doit être coupé, que détruire le bâti pour sortir l’aimant peut s’avérer quasi impossible… l’upgrade lourd est alors une meilleure solution.
Cela fait tout l’intérêt des nouvelles machines comme le Magnetom Flow Ace : plus petit, il peut être installé en passant par des portes hospitalières usuelles, et il ne contient plus que 0,7 litre d’hélium (contre plusieurs centaines dans les machines classiques), dans un circuit fermé étanche. Il n’y a donc plus besoin de construire de cheminée d’évacuation à l’hôpital, et l’appareil supporte le fait de ne pas être réfrigéré pendant longtemps sans que cela n’impacte la quantité d’hélium, ce qui rend possible son transport par bateau, alors que les modèles classiques doivent être expédiés en avion.
Ce type d’approche avec peu d’hélium existe depuis environ 5 ans, elle se développe chez les autres constructeurs et devrait à terme s’imposer pour tous les aimants.
D’après un voyage de presse organisé par Siemens Healthineers
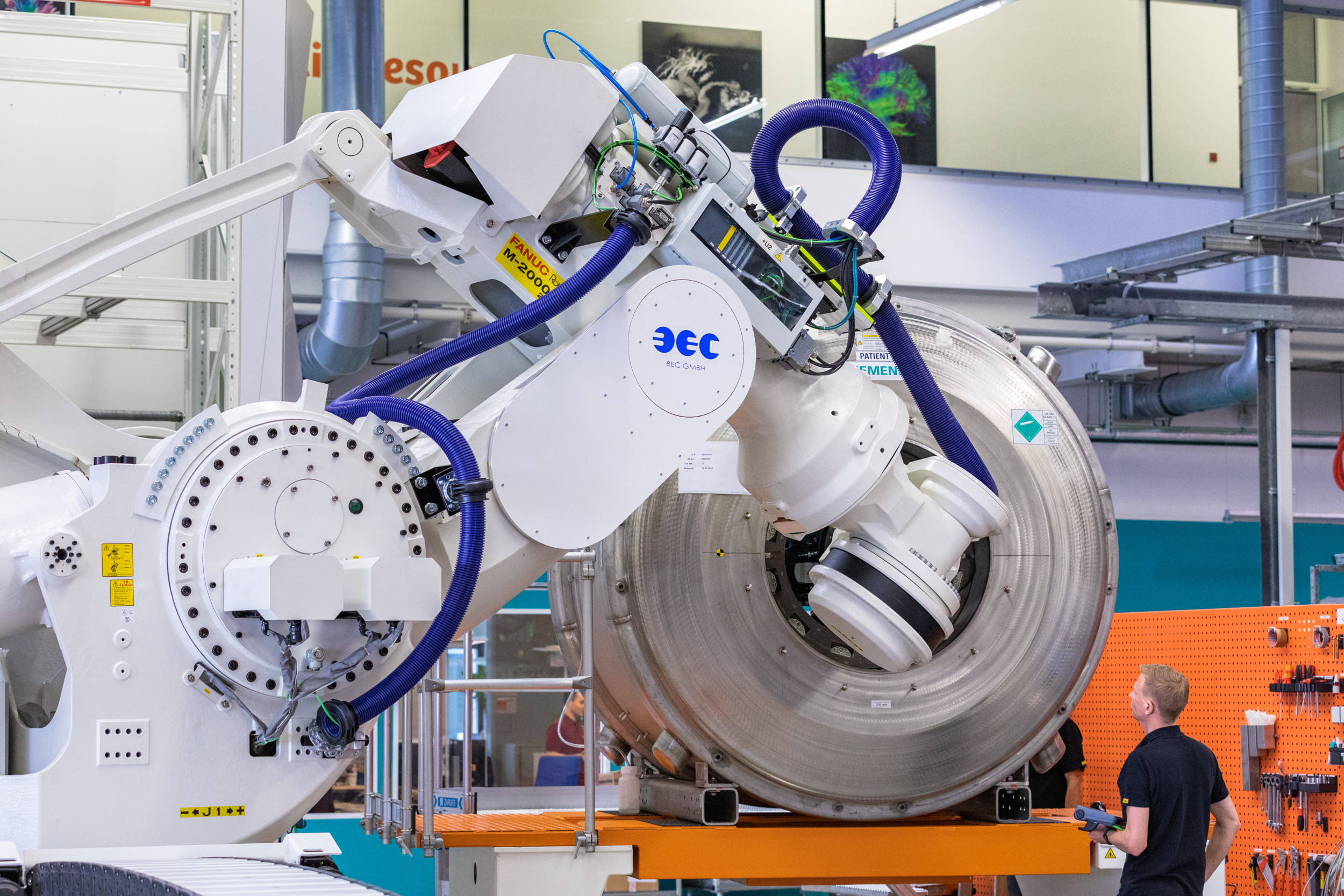
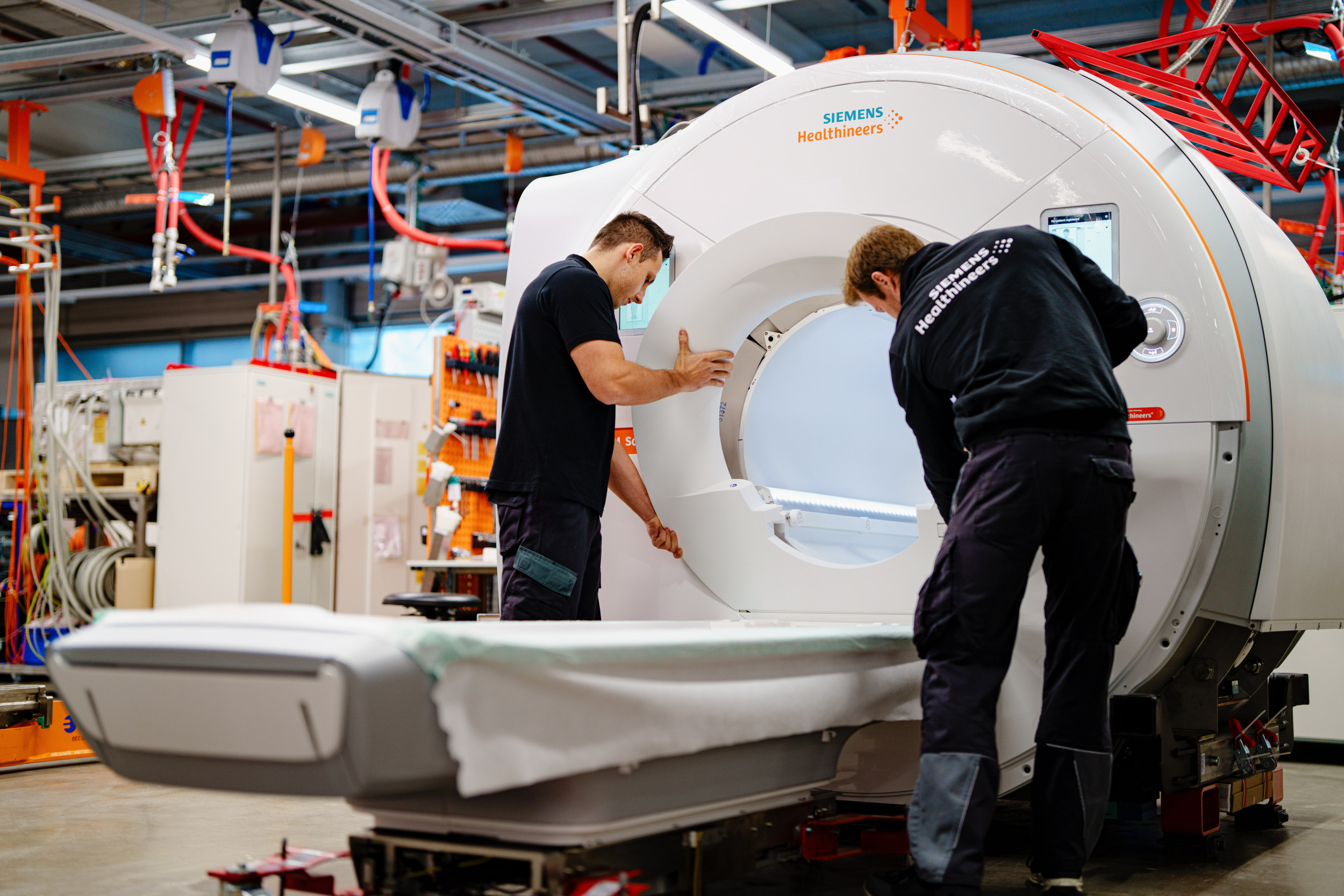
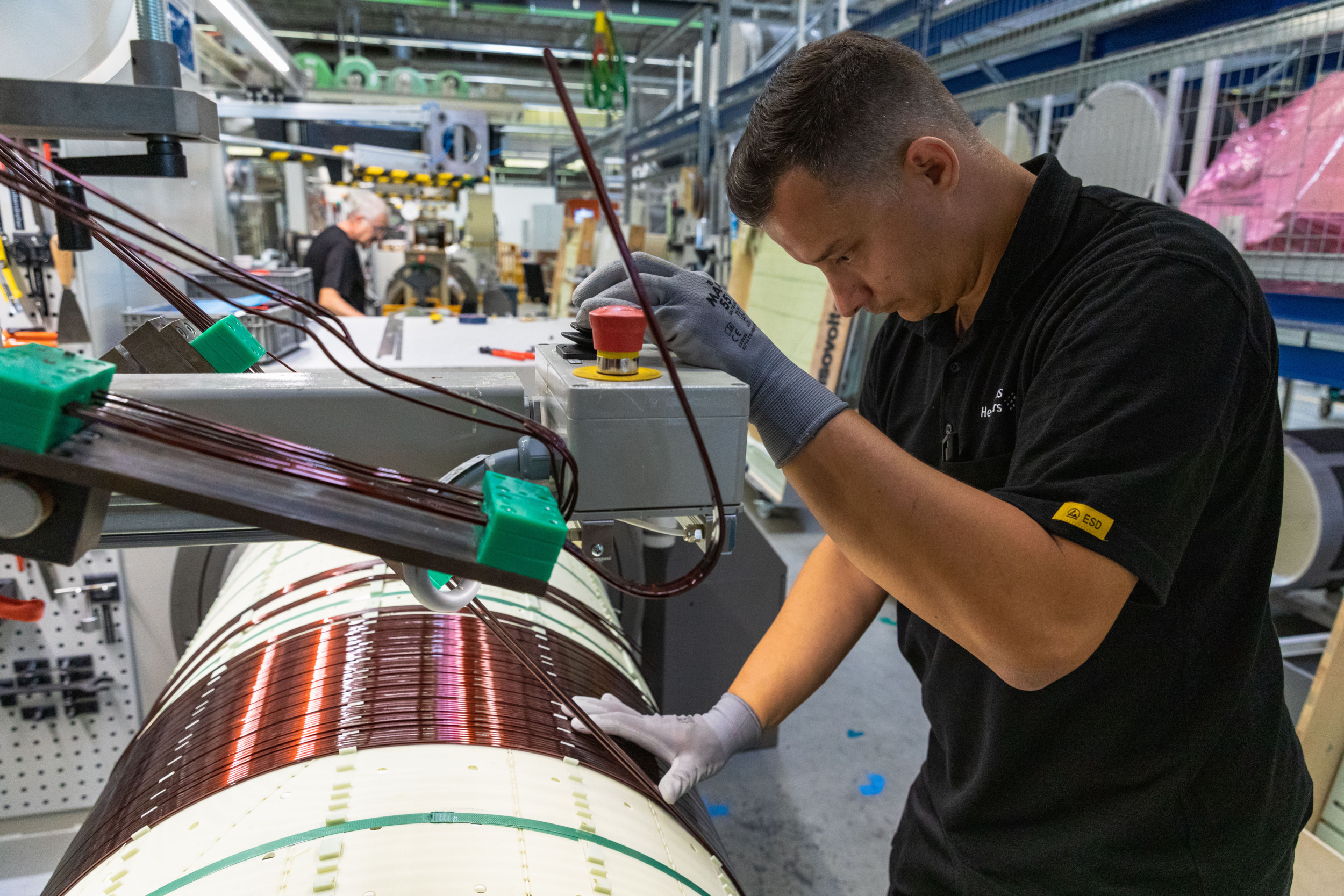
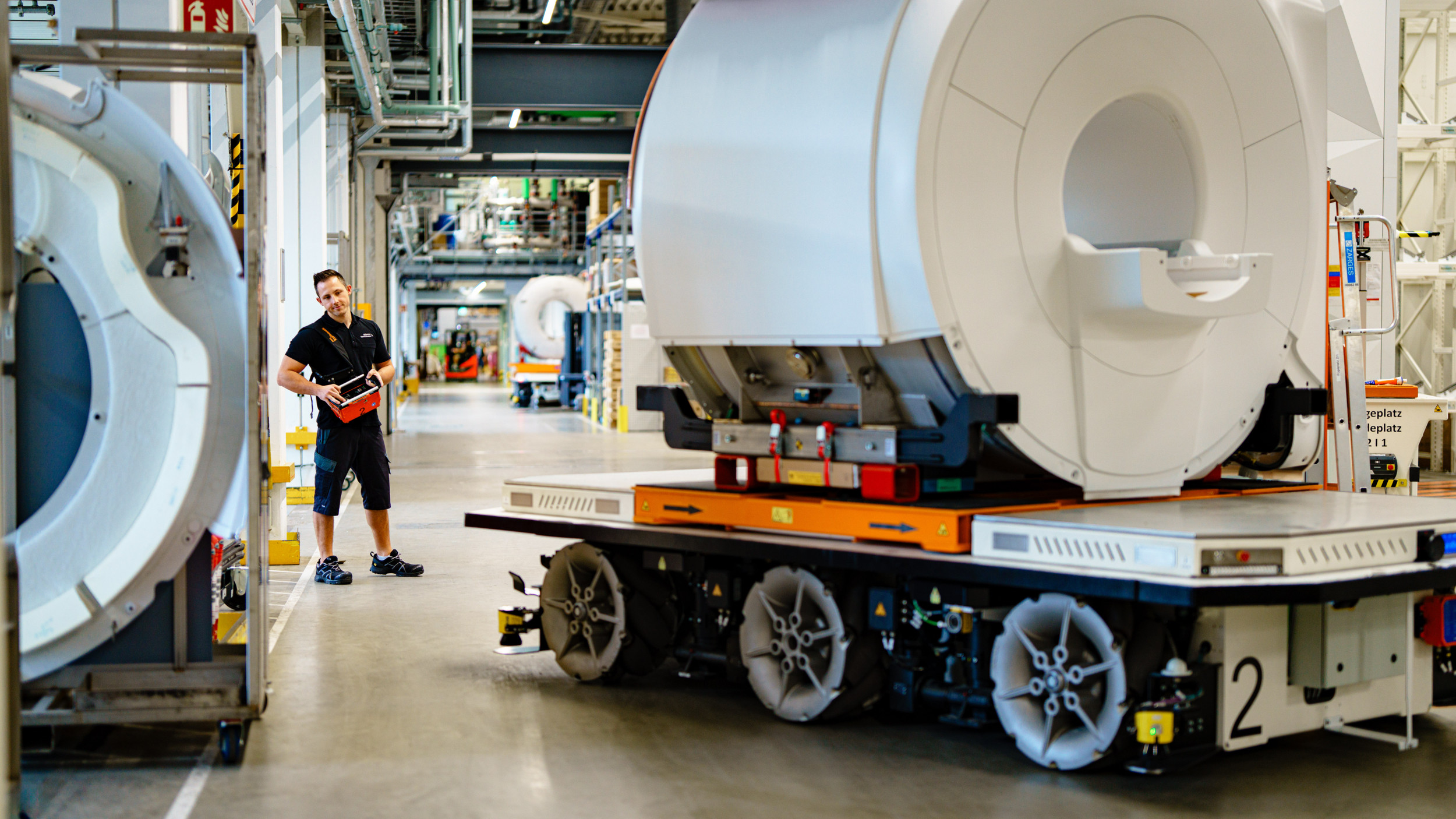
CCAM technique : des trous dans la raquette des revalorisations
Dr Patrick Gasser (Avenir Spé) : « Mon but n’est pas de m’opposer à mes collègues médecins généralistes »
Congrès de la SNFMI 2024 : la médecine interne à la loupe
La nouvelle convention médicale publiée au Journal officiel, le G à 30 euros le 22 décembre 2024